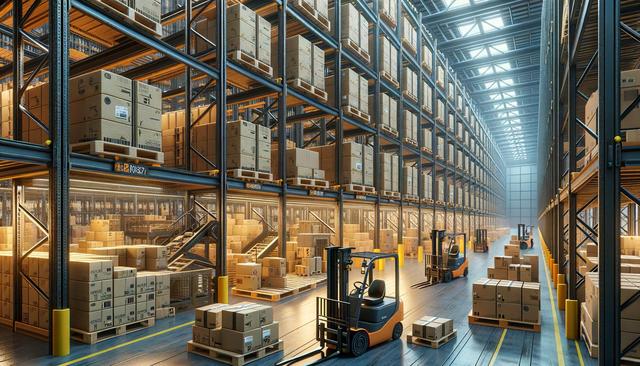
Optimizing Warehouse Picking and Packing for Efficient Order Fulfillment
Understanding the Picking Process in Warehousing
Picking is one of the most crucial stages in warehouse operations, involving the selection of items from inventory to fulfill customer orders. The effectiveness of this process directly impacts delivery times, accuracy, and overall customer satisfaction. There are several methods used in warehouse picking, including piece picking, batch picking, zone picking, and wave picking. Each method has its advantages depending on the size of the operation, the type of products handled, and the volume of orders.
For example, piece picking is ideal for small-scale operations where orders are picked one at a time, while zone picking assigns workers to specific areas of the warehouse, making it suitable for larger facilities. Technology also plays a significant role in enhancing accuracy and speed. Warehouse Management Systems (WMS) can guide pickers efficiently through optimized routes and provide real-time inventory updates, reducing the chance of errors.
Key benefits of optimizing the picking process include:
- Reduced labor costs through efficient workflows
- Improved order accuracy and reduced returns
- Faster order fulfillment and improved customer satisfaction
Streamlining the Packing Process
After items are picked, the packing process ensures that they are securely packaged for shipping. This step involves verifying order accuracy, choosing appropriate packaging materials, and labeling shipments. Efficient packing contributes to reduced damage rates and optimized shipping costs. Proper training and standardized procedures can significantly improve the consistency and reliability of packing teams.
Warehouses often use automated systems such as dimensioners and weigh scales to determine the most cost-effective packaging solutions. Additionally, pack stations should be ergonomically designed and strategically located to minimize movement and fatigue among workers. Incorporating checklists and barcode scanning during the packing process can further enhance accuracy and accountability.
Important aspects to consider when improving packing operations include:
- Selection of packaging material fit for the item type and size
- Implementation of quality control checks before sealing
- Use of automation for labeling and documentation
Integrating Technology to Improve Operations
Technology integration is a game changer in modern warehouse management. Tools such as handheld scanners, mobile apps, and wearable tech help workers access order details and inventory updates in real time. Augmented reality (AR) and voice-directed picking are emerging solutions that guide workers through picking routes with hands-free instructions, improving speed and reducing errors.
Advanced analytics can also be employed to identify bottlenecks and optimize workflows. For instance, a WMS can track metrics like pick rates, packing time, and error frequency, enabling managers to make data-driven decisions. Integration with other systems such as Enterprise Resource Planning (ERP) platforms ensures seamless coordination between inventory, purchasing, and shipping departments.
When integrating technology, warehouses should:
- Ensure staff are properly trained on new systems
- Regularly maintain and update hardware and software
- Choose scalable solutions that can grow with business needs
Training and Workforce Management
Even with advanced technology, human factors remain central to successful warehouse picking and packing. Well-trained staff who understand procedures and safety protocols are less likely to make costly mistakes. Effective workforce management includes hiring skilled personnel, providing regular training, and maintaining high morale through a supportive work environment.
Creating clear job descriptions and performance benchmarks helps employees understand expectations and stay motivated. Shift scheduling should also consider peak demand periods to ensure sufficient coverage without overburdening staff. Encouraging feedback can lead to process improvements and a more engaged workforce.
Key strategies for workforce management include:
- Ongoing training programs on equipment and safety
- Incentive systems to reward accuracy and efficiency
- Cross-training to allow flexibility in task assignments
Measuring Performance and Continuous Improvement
To maintain efficiency in warehouse picking and packing, it’s important to regularly measure performance and seek areas for improvement. Key Performance Indicators (KPIs) such as order accuracy rate, pick time per order, packing time, and return rates provide valuable insights into operational efficiency. Regular audits and feedback loops allow managers to identify issues and implement corrective actions promptly.
Continuous improvement methodologies like Lean and Six Sigma can be applied to streamline workflows, eliminate waste, and enhance productivity. Involving employees in problem-solving initiatives fosters a culture of accountability and innovation. Periodic reviews of layout design, equipment, and processes ensure that the warehouse adapts to changing business needs.
Effective performance management involves:
- Tracking and analyzing relevant KPIs
- Implementing regular reviews and process audits
- Encouraging a culture of feedback and innovation
Conclusion: Building a Resilient Warehouse Operation
Optimizing picking and packing processes is essential for efficient warehouse operations and long-term business success. By leveraging the right combination of technology, training, and continuous improvement practices, businesses can enhance accuracy, reduce costs, and meet customer expectations more consistently. Whether you’re managing a small warehouse or a large distribution center, focusing on these core areas can lead to tangible improvements in performance and service quality.