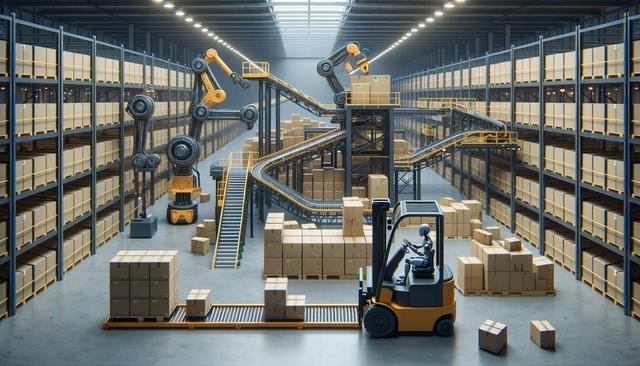
picking e packing de armazém
Understanding Picking and Packing in Warehouse Operations
Picking and packing are two fundamental processes in warehouse logistics that ensure customer orders are accurately selected and prepared for shipment. The ‘picking’ phase involves locating and retrieving the correct items from storage, while ‘packing’ includes safely boxing or wrapping the items, labeling them, and preparing them for delivery. Together, these processes are often referred to as ‘picking e packing de armazém’ in regions where Portuguese is spoken, highlighting their global relevance in supply chain management. Efficient execution of these tasks is essential to maintaining smooth operations and meeting customer expectations.
Types of Picking Strategies
There are several picking strategies used in warehouses, each tailored to suit different types of inventory, order volume, and storage layouts. Choosing the right method can significantly improve speed and accuracy. Common picking strategies include:
- Piece Picking: Picking individual items for each order, ideal for small-scale operations.
- Batch Picking: Collecting items for multiple orders at once to reduce travel time.
- Zone Picking: Assigning workers to specific areas of the warehouse to pick items only from their zones.
- Wave Picking: Coordinating picking and packing based on schedules to optimize shipping times.
Each strategy has its advantages and potential drawbacks, depending on the warehouse’s layout, product variety, and order frequency. Implementing the appropriate strategy can lead to substantial improvements in operational productivity.
Packing Techniques and Best Practices
The packing stage is just as important as picking because it ensures items are protected during transit and reach customers in optimal condition. Effective packing involves selecting the right materials, such as boxes, bubble wrap, or padding, and arranging items to avoid damage. Best practices in packing include:
- Using the smallest possible box that fits all items securely
- Ensuring weight is evenly distributed to maintain package integrity
- Labeling packages clearly with shipping and handling instructions
- Including packing slips or invoices inside the box when required
Technological tools like automated packing machines and packing software can also help reduce errors and increase throughput, especially in high-volume operations.
Technology’s Role in Optimizing Picking and Packing
Modern warehouses increasingly rely on advanced technologies to streamline picking and packing processes. Tools such as barcode scanners, RFID systems, and warehouse management systems (WMS) allow workers to locate items quickly and ensure order accuracy. Mobile picking devices and voice-directed picking systems have also become popular, enabling hands-free operation and reducing training time for new employees. Additionally, automated guided vehicles (AGVs) and robotics are transforming warehouse logistics by handling repetitive tasks, allowing human workers to focus on more complex responsibilities.
Data analytics plays a vital role in identifying bottlenecks and improving decision-making. Real-time tracking and performance dashboards help managers monitor productivity and make data-driven improvements. As warehouses continue to grow in complexity, integrating these technologies becomes increasingly necessary for maintaining competitiveness and efficiency.
Challenges and Solutions in Picking and Packing
Despite technological advancements, warehouses still face several challenges in picking and packing. High order volumes, seasonal spikes, and labor shortages can strain operations. Inaccurate picks, damaged goods, and shipping delays can lead to customer dissatisfaction and increased costs. Some common challenges include:
- Inventory mismanagement leading to stockouts or overstock
- Human error during picking or packing
- Inconsistent packing quality
- Limited space and resource constraints
To address these issues, warehouses can invest in employee training, implement standardized procedures, and conduct regular audits. Continuous improvement initiatives, such as Lean or Six Sigma, can also help identify inefficiencies and enhance overall performance. Collaborating with logistics partners and adopting scalable solutions can further support long-term success.
Conclusion: Enhancing Efficiency Through Smart Picking and Packing
For warehouse operators and logistics managers, mastering the processes of picking and packing is essential to ensuring smooth order fulfillment and delivering excellent customer service. By understanding the various strategies, leveraging technology, and addressing operational challenges proactively, businesses can significantly improve their warehouse performance. Whether dealing with high-volume e-commerce orders or specialized inventory handling, a well-optimized picking and packing system lays the foundation for reliable and scalable supply chain operations.