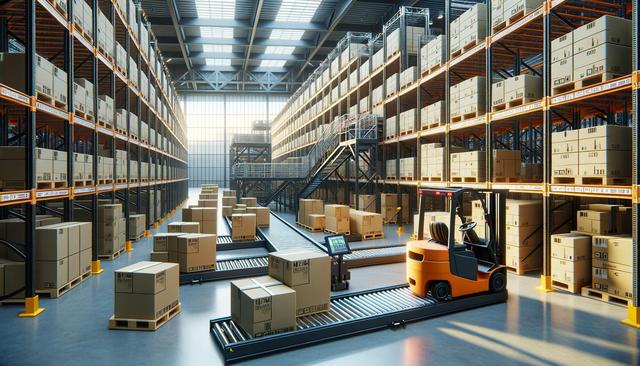
Optimizing Warehouse Picking and Packing for Operational Efficiency
Understanding the Basics of Picking and Packing
Picking and packing are core components of warehouse operations, particularly in fulfillment centers and distribution hubs. While picking refers to the process of retrieving products from inventory to fulfill customer orders, packing involves preparing those items for shipment by securely placing them in packaging, labeling them, and ensuring quality control. Together, these tasks form the backbone of order fulfillment and require careful coordination to maintain speed and accuracy. The effectiveness of these processes plays a pivotal role in how quickly and accurately orders are delivered to end customers, influencing both customer satisfaction and return rates.
There are several picking methods commonly used in warehouses, such as:
- Piece picking – selecting individual items for a single order
- Batch picking – collecting items for multiple orders at once
- Zone picking – assigning pickers to specific areas of the warehouse
- Wave picking – scheduling picking and packing in waves based on shipping schedules
The choice of method depends on factors like order volume, product variety, and warehouse layout. Similarly, packing stations must be designed to ensure ergonomic efficiency, damage prevention, and proper documentation. By understanding these foundational elements, businesses can start to identify areas for improvement and optimization.
Technology’s Role in Modern Picking and Packing
Technology has revolutionized the way warehouses approach picking and packing. Warehouse Management Systems (WMS) now offer real-time inventory tracking, automated picking lists, and route optimization, reducing human error and increasing productivity. Mobile scanning devices and wearable technology ensure that warehouse workers can confirm item codes, record movement, and receive updates without returning to a central station, facilitating faster workflows.
Automation also plays a growing role. Conveyor belts, robotic pickers, and automated guided vehicles (AGVs) can drastically reduce the time spent moving products within the facility. These technologies are especially useful in high-volume environments where even small time savings per order can lead to significant gains.
Benefits of integrating technology into picking and packing include:
- Improved order accuracy and reduced returns
- Faster order fulfillment cycles
- Better labor allocation and efficiency
- Enhanced inventory visibility and control
However, implementing technology requires thoughtful planning, training, and ongoing maintenance. Not all warehouses may benefit equally, making it important to assess needs and scale solutions appropriately.
Designing an Efficient Warehouse Layout
The physical structure of a warehouse significantly impacts how smoothly picking and packing activities flow. A well-organized layout minimizes travel time, reduces congestion, and supports logical product placement. High-frequency items should be placed in easily accessible locations, often near packing stations, to speed up retrieval. Clear signage, wide aisles, and modular shelving also contribute to smoother operations.
Key strategies to consider when designing a warehouse layout include:
- Adopting a logical product zoning system based on item characteristics or order frequency
- Implementing one-way traffic paths to reduce picker collisions and confusion
- Placing packing stations near shipping docks to minimize transport time
- Using vertical space effectively with high-density shelving and mezzanines
Regularly reviewing and adjusting the layout based on changes in product lines or order behavior is essential. Seasonal fluctuations, promotional campaigns, or new inventory can all affect demand patterns, necessitating adjustments to maintain efficiency.
Training and Workforce Management
Behind every successful picking and packing operation is a well-trained and motivated workforce. Given the repetitive and physically demanding nature of the work, employee training and support are critical to maintaining high performance and low error rates. Training should cover not only the mechanics of picking and packing but also the use of warehouse technology, safety protocols, and quality assurance measures.
Effective workforce management includes:
- Regular skill development sessions and cross-training opportunities
- Clear communication channels for reporting issues or suggestions
- Performance monitoring with constructive feedback loops
- Incentive programs to encourage accuracy and speed
Additionally, fostering a positive work culture can significantly impact productivity and retention. Simple enhancements like climate control, access to hydration, and ergonomic equipment can greatly improve the working conditions for warehouse staff.
Measuring and Improving Performance
To continuously enhance picking and packing operations, it’s important to track performance metrics and use data to guide decisions. Key performance indicators (KPIs) such as pick rate, order accuracy, packing time per order, and return rates provide valuable insights into workflow efficiency and employee productivity. Benchmarking these metrics over time helps identify bottlenecks and areas for process refinement.
Strategies for ongoing improvement may include:
- Conducting regular process audits and time-motion studies
- Testing new picking methods or warehouse configurations
- Soliciting feedback from staff on pain points and improvement ideas
- Implementing lean principles to eliminate waste and streamline operations
Improvement is an iterative process. Small changes, when guided by accurate data and thoughtful planning, can yield meaningful improvements in efficiency, cost savings, and customer satisfaction.
Conclusion: Building a Resilient Fulfillment Operation
For businesses aiming to stay competitive in an increasingly fast-paced marketplace, optimizing warehouse picking and packing is essential. From layout planning and workforce training to technology integration and performance tracking, each element contributes to a cohesive and efficient fulfillment strategy. By investing in these areas, warehouse managers can reduce operational costs, improve order accuracy, and deliver better service to customers. A resilient and responsive picking and packing system not only supports daily operations but also positions a business to scale and adapt to future logistics challenges.