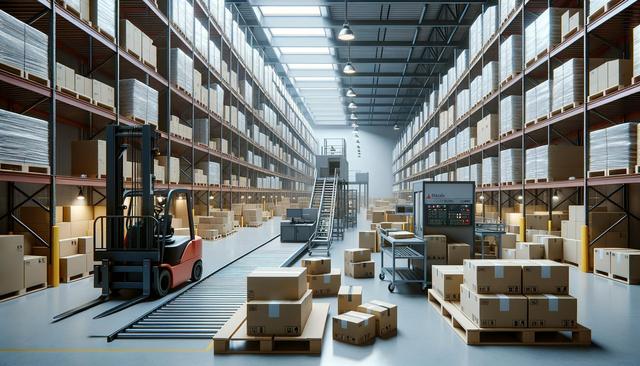
picking e packing de armazém
Understanding the Basics of Picking and Packing
Picking and packing are two fundamental processes in warehouse operations that directly impact the speed and accuracy of order fulfillment. ‘Picking’ refers to the process of collecting products from storage locations to fulfill customer orders, while ‘packing’ involves preparing those items for shipment, ensuring they are secure and labeled correctly. Together, these processes form a critical link between inventory management and distribution. Businesses that optimize their ‘picking e packing de armazém’ strategies often experience improved operational efficiency and reduced error rates, making these functions central to supply chain performance.
There are several picking methods used in warehouses, including:
- Single order picking – picking one order at a time, suitable for low-volume operations.
- Batch picking – collecting items for multiple orders simultaneously to minimize travel time.
- Zone picking – assigning workers to specific areas of the warehouse to focus their efforts.
- Wave picking – combining elements of batch and zone picking, coordinated by specific time intervals.
The packing process typically involves verifying order accuracy, choosing appropriate packaging materials, and labeling packages for delivery. Each step must be handled with care to avoid damage during transit and to ensure customer satisfaction.
The Role of Technology in Warehouse Operations
Technology plays a transformative role in modern warehouse picking and packing. From barcode scanners to warehouse management systems (WMS), digital tools help streamline operations, reduce human error, and improve overall accuracy. A well-integrated WMS can provide real-time inventory tracking, optimize picking routes, and automate packing instructions, which are essential in high-volume environments.
Some key technologies enhancing ‘picking e packing de armazém’ include:
- RFID systems for faster and more accurate inventory identification.
- Voice-directed picking tools that guide workers through tasks via audio prompts.
- Automated storage and retrieval systems (AS/RS) that reduce manual handling.
- Mobile workstations that allow packing staff to move efficiently around the warehouse.
By leveraging these tools, warehouses can not only improve operational efficiency but also scale their processes to meet growing demand without compromising accuracy or delivery speed.
Warehouse Layout and Process Optimization
Effective warehouse layout design is crucial for optimizing picking and packing operations. A poorly organized space can lead to longer travel times, higher labor costs, and increased errors. Conversely, a well-structured layout supports workflow efficiency and enhances productivity. Elements such as aisle width, shelf placement, and item categorization all play a role in how smoothly operations run.
To optimize ‘picking e packing de armazém’, consider the following layout strategies:
- Place high-demand items near packing stations to reduce travel time.
- Use clear signage and labels to guide workers efficiently.
- Implement standardized storage bins and shelf heights for consistency.
- Create separate zones for receiving, picking, packing, and shipping to avoid congestion.
Continuous monitoring and adjustment of layout and procedures are necessary as product lines and order volumes change. Regular audits and employee feedback can help identify areas for improvement.
Training and Workforce Management
A skilled and well-managed workforce is essential to the success of warehouse operations. Training programs should be thorough and ongoing, emphasizing accuracy, safety, and efficiency in picking and packing tasks. Clear communication and defined responsibilities help ensure that every team member understands their role in the process.
Key training areas might include:
- Proper use of picking technology and equipment.
- Best practices for packing fragile or hazardous items.
- Time management and prioritization techniques.
- Safety protocols for lifting and material handling.
Employee performance can be supported through incentive programs, regular feedback, and opportunities for advancement. When workers feel valued and are equipped with the right tools and knowledge, they are more likely to perform their duties efficiently and accurately.
Measuring Performance and Continuous Improvement
To ensure the effectiveness of picking and packing processes, it’s important to regularly measure performance using key metrics. These insights allow warehouse managers to identify trends, uncover inefficiencies, and implement changes that improve productivity and accuracy. Some common metrics include order picking accuracy, average order processing time, and packing error rates.
Strategies for continuous improvement in ‘picking e packing de armazém’ include:
- Conducting time and motion studies to streamline workflows.
- Implementing feedback loops between warehouse staff and management.
- Regularly updating technologies and revising procedures as needed.
- Benchmarking against industry standards to maintain competitive performance.
Continuous improvement is not a one-time effort but an ongoing commitment to operational excellence. Through consistent measurement and adaptability, warehouses can evolve to meet the changing demands of customers and markets.
Conclusion: Enhancing Efficiency in Picking and Packing
For businesses involved in warehousing and logistics, the picking and packing process is more than just a routine task—it’s a vital component of customer satisfaction and operational success. By understanding the fundamentals, investing in the right technologies, optimizing layouts, training staff, and committing to continuous improvement, organizations can create a streamlined and accurate order fulfillment process. Prioritizing efficiency in ‘picking e packing de armazém’ ultimately leads to lower costs, faster shipping times, and stronger customer relationships.